Our client is the world’s leading logistics company, with a workforce of 380,000 people across over 220 countries and territories. They facilitate cross-border trade, reach new markets and deliver approximately 1.8 billion parcels annually.
The Challenge
Space optimization and energy efficiency
Our client operated a state-of-the-art showcase site in the UK. However, challenges included:
- Space requirements: The volume of space required for operations was substantial, leading to inefficiencies and increased operational costs
- Energy consumption: High energy consumption was incurred due to operating procedures aimed at maintaining personnel comfort, despite low throughput volume
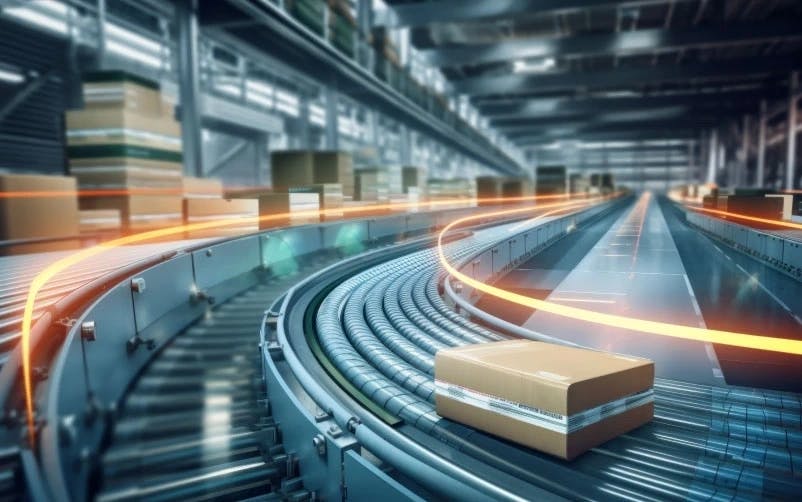
The Objective
Optimizing warehouse operations
The primary objective was to implement a fully automated stacker crane system to manage the storage and retrieval of palletized goods in the double-deep high bay warehouse.
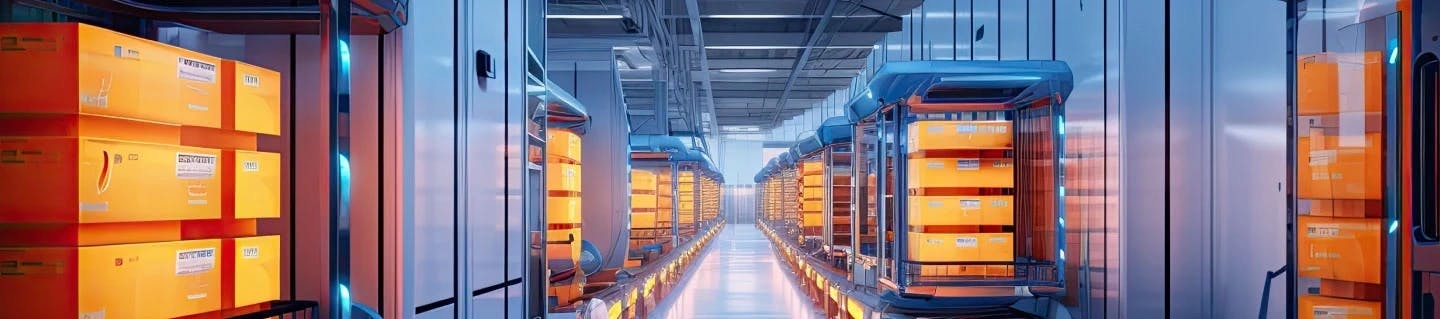
The Solution
Maximizing warehouse efficiency
The automation solution was delivered by Swisslog and integrated into Blue Yonder Warehouse Management System (WMS). Key components of the solution included:
- Fully automated stacker crane: The stacker crane provided all movements for storage and retrieval of palletized goods in the double-deep high bay warehouse, optimizing space utilization
- Automated conveyor pallet system (ASRS): Pallets were fed into 13 high bay cranes via an automated conveyor pallet system. The cranes moved the pallets into double-deep storage locations, maximizing storage capacity
- Integration development: Ground-up development of APIs and transactional messages, including part master, induction, movement requests, confirmations, pick requests, cancellations, error handling, inventory attribute changes, product removal and inventory reconciliation. Integration was facilitated through Blue Yonder’s integrator and standard WCS module communication
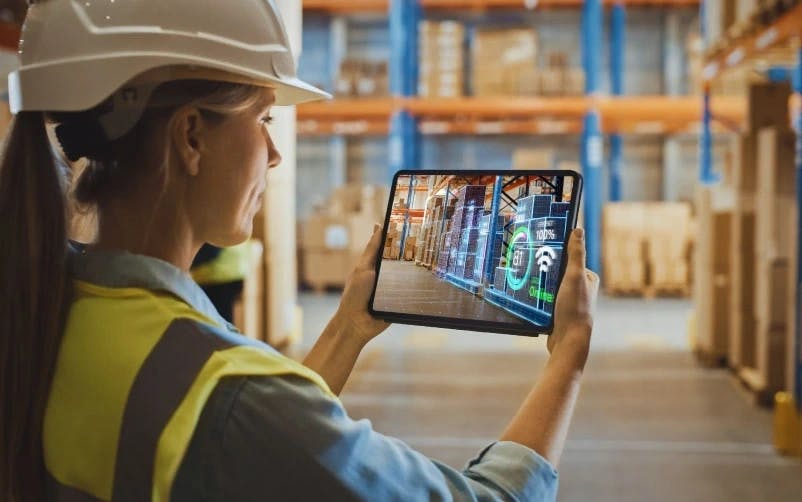
The Impact
Automated system enhances throughput, space and energy efficiency
Our client has revolutionized warehouse operations and delivered tangible benefits in efficiency, space optimization and energy consumption reduction. The implementation of the automated stacker crane system resulted in significant business benefits:
- Increased throughput volume: The solution provided a high throughput volume, optimizing warehouse operations and enhancing overall efficiency
- Space optimization: The compact double-deep storage footprint minimized space requirements, leading to improved space utilization and cost savings
- Reduced energy consumption: Up to a 25% decrease in energy consumption was achieved due to lower operating temperatures (elimination of heating for personnel) and operation in dark spaces
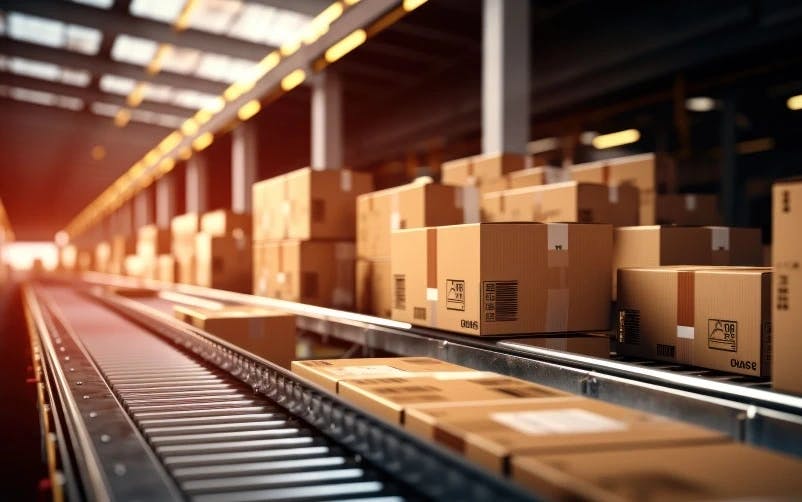